Top size and power saving benefits of programmable timing
Programmability improves electronic product design in several ways. Some benefits are more obvious, such as faster development and shorter lead times. Some are performance related, as discussed in the first blog in this series. Other benefits, which we dive into below, lead to decreased size and power in somewhat surprising, lesser known ways. All of these advantages are enabled by the extensive feature set (many shown in the table below) and programmable architecture of MEMS timing systems.
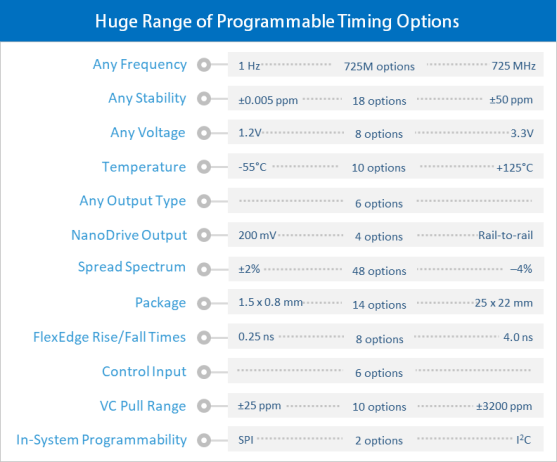
Smaller size, bigger features
A programmable timing platform can reduce component count and system size in a number of ways. For starters, because the frequency of our devices can be programmed over a very wide range with six decimals of accuracy, designers can select an output frequency that matches the downstream chip (MCU, MPU, SoC, etc.) requirements exactly, eliminating the need for extra buffer/frequency dividers and frequency translator PLLs. Some oscillators have in-system programmability (ISP) that allows the frequency to be programmed from 1 MHz to 725 MHz during operation. These oscillators can also be pulled up to ±3200 ppm with 5 ppt resolution and excellent pull linearity. This type of programmable device is ideal for replacing multiple timing components in systems that support more than one frequency.
Another BOM-reducing practice is to program the oscillator output driver to its maximum drive strength, enabling it to drive multiple devices. This eliminates the need for a fanout buffer and reduces the number of required timing components. For example in a small form factor wireless product, a single 32-kHz oscillator with higher drive strength can drive the RTC processor, the BLE sleep clock, and an audio DAC or codec, replacing several crystals and all of their associated load capacitors. And there are no worries about signal integrity or reflection issues since the rise/fall time of these 32-kHz oscillators ranges from 10s to 100s of ns depending on the device family.
MEMS are inherently small and robust, and don’t require bulky packaging. Because the internals of a MEMS oscillator are all silicon, they can be packaged using the latest advanced semiconductor packaging technologies including chip scale packaging (CSP). A designer can select an oscillator configuration in a CSP where the footprint is no larger than the IC oscillator die, measuring just 1.5 x 0.8 mm—the footprint of the smallest oscillators available today.
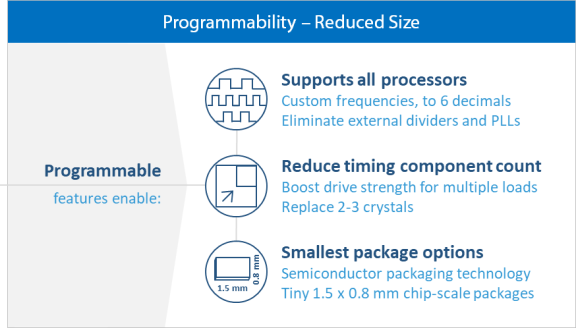
Longer battery life
Lowering power consumption continues to be increasingly more important—and programmable timing features also help in this capacity. Programmable NanoDrive™ is one such feature. With NanoDrive, the output and associated voltage swing can be programmed to match the downstream MCU or PMIC, from full LVCMOS (rail-to-rail) all the way down to an output swing of just 200 mV, significantly lowering current draw. Why use a full LVCMOS output to connect to the oscillator sustaining circuit of a low-power MCU or IC that uses a smaller voltage?
This same oscillator can increase battery life with a wide supply voltage operating range as low as 1.2V, which is ideal for battery powered applications such as coin-cell or super-cap battery backup. And because the frequency of SiTime MEMS oscillators can be programmed down to 1 Hz, the output load current can be dropped to the lower end of the MCU/IC operating frequency range to reduce power consumption (power dissipation is proportional to C*V2*F where C is capacitance, V is voltage and F is frequency). For example, reducing the output frequency from 2 MHz to 500 kHz decreases the unloaded operating current by about 70%. In contrast, quartz crystals are physically larger at lower frequencies, so quartz devices with frequencies less than 32.768 kHz are very uncommon. Using lower frequency MEMS oscillators in combination with low supply voltage and NanoDrive output is a potent combination for dramatically reducing power.

Another means to reduce system power is to select a better frequency stability option, such as a 32-kHz MEMS oscillator with 75 ppm frequency stability, or a 32-kHz MEMS TCXO with stability as good as ±3 ppm. For instance in wireless devices, better stability enables better sleep clock accuracy (SCA) which is directly related to the time a device can stay in sleep state and conserve power. In contrast, using a clock with worse stability causes the radio receiver to turn on earlier and stay on longer to avoid missing packets from the master, causing the system to draw more power. Read more about reducing power through better stability in these white papers: MEMS Timekeeper Extends Standby Life of Mobile Devices and Field Programmable Timing Solutions for Medical Applications.
Lastly, one more way to conserve power is to program the feature pin 1, available in SiTime MHz oscillators. This pin can be programmed to either output enable (OE) or standby (ST). In both cases pulling pin 1 Low stops the output oscillation. With OE the output driver is disabled and put into Hi-Z mode, but the rest of the device is still running. Power consumption decreases due to the inactivity of the output. When the OE pin is pulled back to High, the output is typically activated in < 1 µs. With ST, all internal circuits of the device turn off and power is reduced to a standby current, typically in the range of a few micro Amps. When ST is pulled back to High, the device output resumes within about 3 to 10 ms.
Flexible, programmable timing
Smaller size goes hand-in-hand with lower power in battery-powered products. MEMS timing systems offer the biggest selection of configurable timing features for reducing size and power. In addition, the programmable platform and rich features of SiTime MEMS timing systems improve performance and speed development and manufacturing time while reducing risk. Look for our next blog, the third in the series, to learn more about the top supply chain benefits of programmable timing. In the meantime, check out our part number generator to see the programmable options that spawn hundreds of millions of part numbers.
………………………………………………………
Thanks to Jim Holbrook, Director of Customer Engineering, for his contributions to this article.