MEMS vs Quartz Crystal Oscillators: Benefits, Reliability & Applications
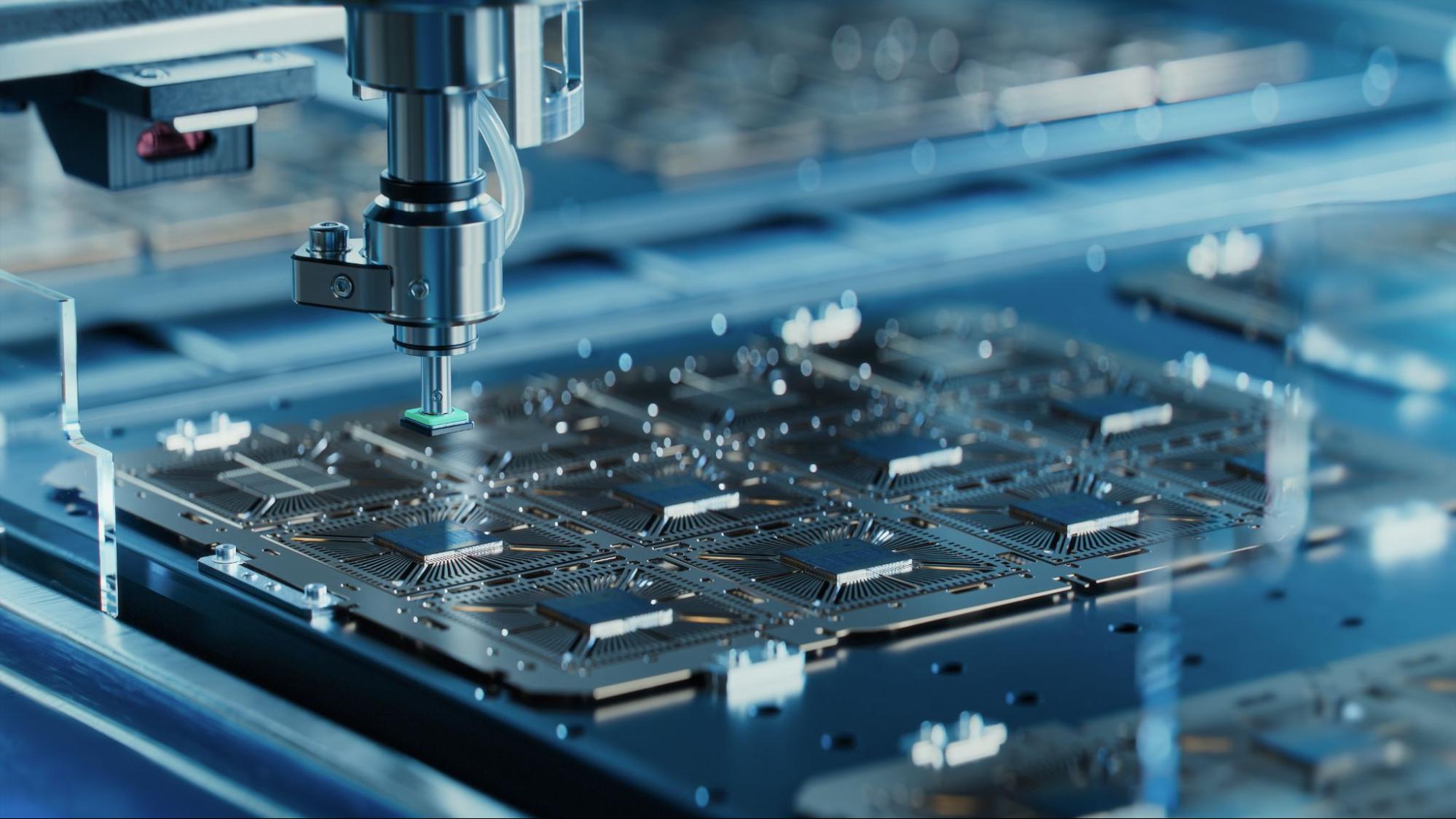
Advanced semiconductor manufacturing processes ensure precision and reliability in modern electronic components
Technical Comparison: How MEMS Oscillators Outperform Quartz
System Integration and Key Applications
Cost, Scalability, and Supply Chain Benefits
Market Trends and the Future of Precision Timing
MEMS Oscillator vs. Quartz Crystal FAQs
SiTime’s precision timing technology is the heartbeat of advanced electronic systems. Its programmable, silicon-based micro-electro-mechanical system (MEMS) oscillators offer higher performance, a smaller footprint, lower power consumption, and greater reliability than quartz-based solutions. Precision timing is increasingly crucial for high-performance applications demanding microsecond- to nanosecond-level accuracy, including AI data centers, aerospace and defense platforms, and advanced driver-assistance systems (ADAS).
This article explores how MEMS oscillators surpass quartz in performance, reliability, and environmental resilience. It also covers system integration and key applications, as well as cost, scalability, and supply chain benefits. Lastly, the article discusses MEMS oscillator market trends and reviews frequently asked questions (FAQs) for system designers.
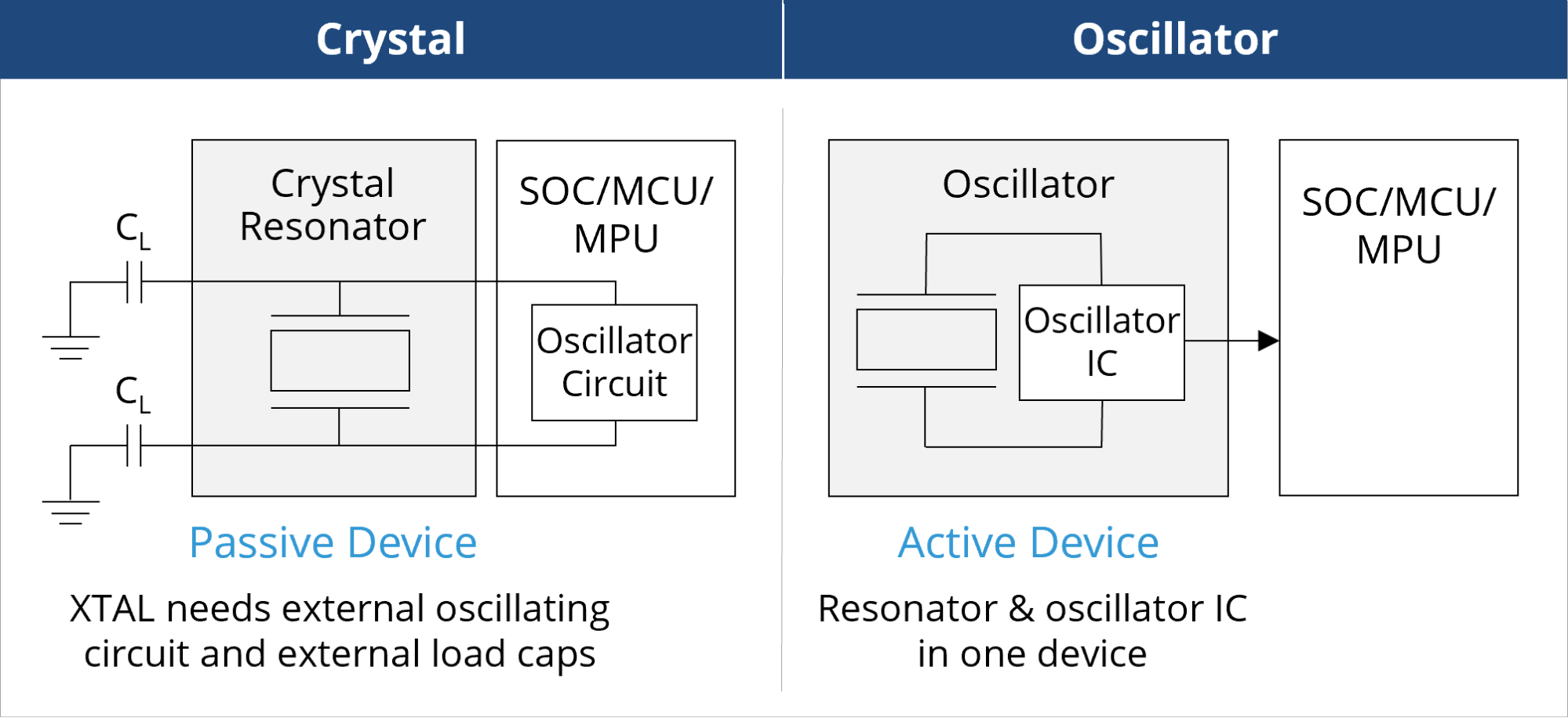
Comparison of MEMS Oscillator vs. Quartz Crystal: Active integrated MEMS oscillator eliminates external components required by passive quartz crystals
Technical Comparison: How MEMS Oscillators Outperform Quartz
Frequency Stability and Accuracy
Silicon-based MEMS oscillators offer key advantages over quartz in frequency accuracy, phase noise stability, and resilience to environmental stressors. High-end MEMS oscillators, such as SiTime’s Super-TCXOs, achieve frequency stability comparable to or better than quartz-based TCXOs, particularly in fluctuating temperatures. Digital frequency tuning and real-time temperature compensation maintain stability in extreme conditions, minimizing frequency drift and long-term aging effects. MEMS oscillators also provide superior phase noise stability in high-vibration environments, where quartz may degrade due to mechanical stress. Unlike quartz, which is prone to frequency shifts from environmental factors, MEMS solutions demonstrate lower failure rates and extended operational lifespans.
Reliability and Long-Term Performance
Quartz oscillators are mechanically fragile and prone to frequency drift over time. Their larger mass and crystalline structure make them susceptible to cracking and frequency shifts. They are also more likely to fail under shock, vibration, and extreme environmental conditions. These limitations increase system downtime and maintenance costs, particularly in mission-critical applications.
In contrast, MEMS oscillators use resonators up to 1,000 times smaller and lighter than quartz crystals, significantly improving resilience to mechanical stress and environmental changes. SiTime’s Epi-Seal® process further bolsters reliability by encapsulating MEMS resonators in a hermetically sealed, pure-silicon vacuum, protecting against moisture, particulate contamination, and long-term degradation.
With failure rates up to 50 times lower than quartz, MEMS oscillators significantly extend operational lifespans, reduce recalibration needs, and lower system maintenance costs—providing a cost-effective, long-term timing solution for high-performance, mission-critical applications.
System Integration and Key Applications
Whether for mission-critical systems or consumer devices, engineers must balance multiple design tradeoffs and constraints, including:
- Compact Footprint & Miniaturization: As device sizes decrease, component miniaturization is essential for board layout optimization and system integration. MEMS oscillators, significantly smaller than quartz, enable more compact designs and easier placement in miniaturized systems.
- Power Efficiency: Battery-operated wearables and edge IoT devices require low-power components to extend operational life while supporting expanding feature sets. MEMS oscillators facilitate ultra-low-power operation through programmable output voltage and dynamic frequency control, optimizing energy consumption. MEMS oscillators can reduce power consumption by 30–50% compared to quartz crystal (XTAL) + SoC oscillators.
- Electromagnetic Interference (EMI): Reliable performance requires timing solutions that minimize EMI and maintain signal integrity in complex electronic environments with densely packed components. MEMS oscillators incorporate programmable drive strength and spread spectrum clocking, mitigating EMI concerns without additional shielding or filtering. Notably, MEMS oscillators provide up to 35 dB better EMI immunity than quartz oscillators in differential configurations.
Selecting the right timing solution is crucial to overcoming these design tradeoffs and constraints. Quartz oscillators have inherent limitations in size, fragility, and integration flexibility. MEMS oscillators, in contrast, offer compactness, vibration resistance, and seamless integration with modern semiconductor packages. Their native silicon-silicon compatibility eliminates the need for quartz compensation circuits and tuning, simplifying circuit design and optimizing manufacturing scalability.
Silicon-based MEMS oscillators support a wide range of high-performance applications, including:
- AI Datacenters: AI and ML are driving a tenfold increase in data center throughput, with optical modules now supporting 800 Gbps Ethernet connectivity. This surge in data processing demands scalable advancements in timing performance and reliability, particularly in high-temperature environments. AI accelerator clusters rely on precise synchronization and high-bandwidth interconnects to minimize latency, maximize efficiency, and reduce total cost of ownership (TCO). High-performance MEMS oscillators improve synchronization accuracy, reduce jitter, and enable real-time telemetry, enhancing network stability and overall performance.
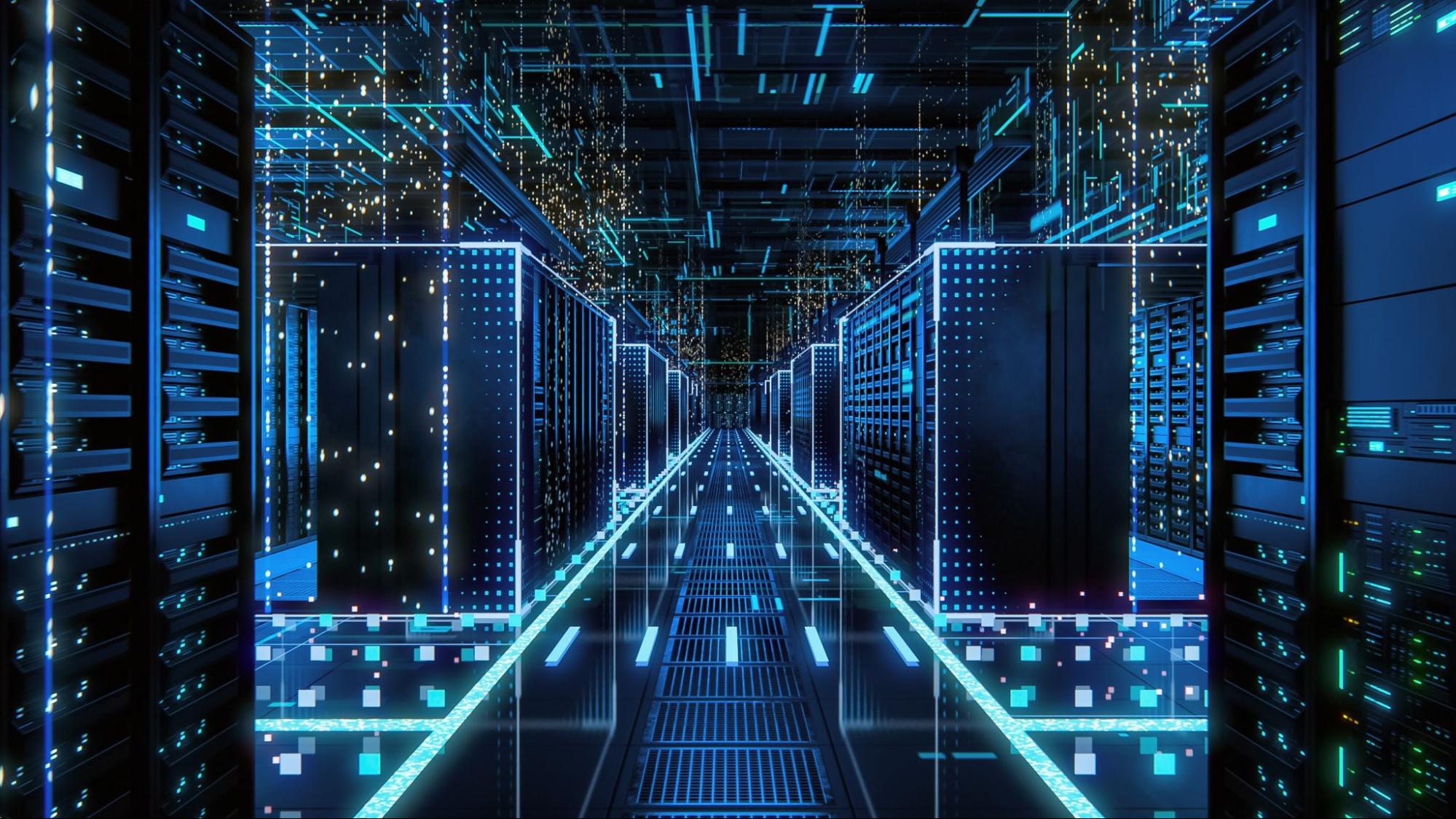
High-performance data centers rely on precision timing to ensure synchronization and optimal network performance
- Aerospace and Defense: Mission-critical systems in satellites, aircraft, and navigation platforms require high-reliability timing in space-constrained, high-shock, and high-vibration, aerospace and defense environments. MEMS oscillators deliver precision timing, exceptional stability, reduced acceleration sensitivity, and long-term reliability, ensuring seamless operation even in extreme conditions.
- Communications: 5G networks need 10X greater timing accuracy than 4G to support higher frequencies, denser deployments, and edge computing. Small cells and base stations must maintain precise synchronization in harsh outdoor environments, where vibration, EMI, and temperature fluctuations can degrade performance. MEMS oscillators support IEEE 1588v2 Precision Time Protocol (PTP), stabilize networks by withstanding extreme conditions, minimize signal degradation, and ensure seamless connectivity.
- Mobile and IoT Devices: The growing adoption of consumer and industrial IoT (IIoT) drives demand for compact, power-efficient timing solutions. MEMS oscillators reduce footprint, enhance reliability, and lower power consumption, extending battery life in wearables, smartphones, smart home devices, and IIoT applications.
- Automotive: Electric vehicles (EVs) and ADAS depend on precision timing for safety, sensor fusion, and real-time decision-making. MEMS oscillators—built on resonators 1,000 to 3,000 times lighter than quartz—offer higher vibration resilience while supporting space-constrained automotive designs that require up to 70 timing chips per vehicle. These solutions optimize real-time data processing and collision avoidance, critical for ADAS functionality.
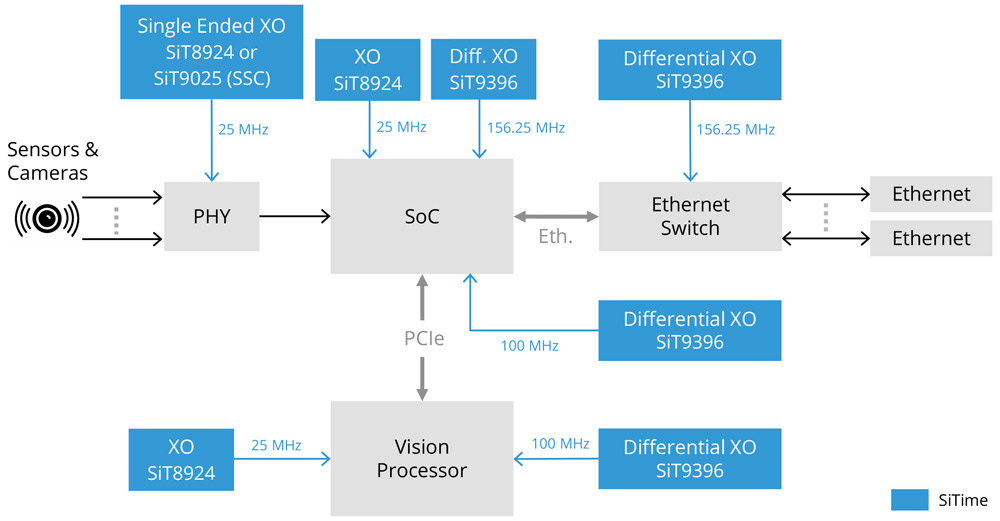
SiTime MEMS Oscillators in Advanced Driver-Assistance Systems (ADAS): Precision timing solutions for SoCs, Ethernet switches, and vision processors
Cost, Scalability, and Supply Chain Benefits
At first glance, quartz oscillators appear to have a lower unit cost than MEMS. However, a comprehensive life cycle cost analysis confirms the long-term expenses associated with quartz:
- Up-Front Engineering Costs: While all timing devices require meticulous circuit design, quartz oscillators often demand additional steps—such as circuit matching and external load capacitor selection—that increase complexity and lengthen development and verification cycles. In contrast, MEMS oscillators support silicon-to-silicon integration, streamlining implementation.
- Manufacturing Constraints: Each quartz oscillator frequency requires a specific crystal cut, increasing production lead times and inventory costs.
- Operational Expenses: Quartz devices have higher failure rates due to mechanical fragility, increasing maintenance costs, and system downtime. SiTime MEMS oscillators achieve failure rates below one defective part per million (DPPM) and exceed two billion hours mean time between failures (MTBF)—up to 50X better than quartz.
In summary, although system designers may pay more initially for MEMS oscillators, they ultimately benefit from lower lifecycle costs, higher system reliability, and an optimal user experience.
Scalability and Manufacturing Efficiency
MEMS oscillators leverage standard silicon fabrication for high-volume, scalable production within the existing semiconductor supply chain and ecosystem. Unlike quartz, which requires specialized manufacturing, MEMS oscillators are programmable to any frequency, streamlining design cycles, reducing lead times, and minimizing SKUs and supply chain disruptions. A single programmable MEMS oscillator can replace multiple quartz SKUs, simplifying procurement and lowering supply-chain risk. With greater environmental resilience, MEMS oscillators improve system durability, reducing costly replacements and maintenance.
Market Trends and the Future of Precision Timing
System designers increasingly rely on precision timing solutions to support faster speeds, always-on connectivity, and growing system complexity. Silicon-based MEMS oscillators meet these demands with resilient, power-efficient, and scalable alternatives to quartz. AI data centers, for example, depend on MEMS oscillators for high-precision, low-jitter timing to synchronize compute clusters, optimize workload distribution, and enable ultra-high-speed networking. Similarly, aerospace, automotive, and communications industries leverage MEMS oscillators to ensure ultra-reliable timing for real-time processing and seamless data transmission in challenging environments.
Breakthroughs in sub-picosecond jitter, AI-driven self-tuning, and deeper system-on-chip (SoC) integration are accelerating MEMS adoption in high-performance applications. At the same time, advances in wafer-level chip-scale packaging (WL-CSP) simplify integration into high-density systems, while real-time temperature compensation and digital frequency tuning enhance stability in dynamic conditions. SiTime’s Super-TCXO and Chorus™ clock generators continue pushing performance boundaries, reinforcing MEMS as the future of intelligent, high-performance timing technology.
MEMS oscillators leverage scalable semiconductor fabrication, reduce lead times, simplify inventory management, and enhance reliability.
MEMS Oscillator vs. Quartz Crystal FAQs
Selecting the right timing solution helps system designers achieve the best combination of performance, reliability, and cost. This FAQ highlights key technical distinctions between MEMS and quartz oscillators.
What is the difference between quartz and MEMS oscillators?
Quartz crystal oscillators generate stable frequencies through the mechanical resonance of a quartz crystal. However, they are physically larger than MEMS oscillators, more fragile, and require additional circuitry for compensation and tuning. MEMS oscillators, built with silicon-based resonators using advanced semiconductor manufacturing techniques, offer greater reliability, a smaller footprint, and higher programmability, positioning them as the preferred choice for high-performance electronic systems.
Are MEMS oscillators more accurate than quartz?
High-end MEMS oscillators, such as SiTime’s Super-TCXO, offer frequency stability comparable to or better than quartz-based TCXOs, particularly in environments with temperature fluctuations. Advanced MEMS timing solutions incorporate real-time temperature compensation and digital frequency tuning, maintaining sub-ppm accuracy even in the most demanding conditions.
How do MEMS oscillators perform in extreme temperatures and harsh environments?
MEMS oscillators offer superior temperature stability, shock resistance, and vibration resilience compared to quartz. Quartz oscillators are prone to frequency shifts under environmental stress, while MEMS resonators—protected by semiconductor-grade encapsulation, such as SiTime’s Epi-Seal® process—maintain consistent performance in aerospace and defense, industrial, and automotive applications.
Do MEMS oscillators offer phase noise performance comparable to quartz?
In many high-performance applications, such as AI data centers, high-speed networking, and communications, premium MEMS oscillators provide competitive phase noise while offering clear advantages in size, reliability, and integration.
Are MEMS oscillators more expensive than quartz?
Not necessarily. While quartz devices may have a lower up-front unit cost, MEMS oscillators reduce TCO over time by minimizing engineering effort, manufacturing complexity, and failure rates. They also simplify inventory management, replace multiple quartz SKUs, and lower long-term operational costs through higher reliability and an extended lifespan.
How do MEMS and quartz oscillators compare in power consumption?
Power consumption varies by type and application. Some quartz oscillators consume less power than MEMS alternatives. However, silicon-based MEMS technology enables power-saving features such as programmable voltage swing (NanoDrive™), dynamic frequency scaling, and adjustable output drive strength. These features optimize energy efficiency and extend operational life in battery-powered applications like smartphones, IoT devices, and wearables.
Can MEMS oscillators replace quartz in all applications?
In most cases, yes. MEMS oscillators are steadily replacing quartz in high-performance applications—including AI data centers, telecommunications, ADAS, smartphones, and wearables—thanks to their superior integration, scalability, and reliability. However, quartz may remain in lower- to medium-performance applications that don’t require precision timing, programmability, or real-time adaptability to dynamic environmental conditions. Additionally, certain niche applications demanding ultra-low phase noise and jitter—particularly in the femtosecond range, such as specialized RF and test and measurement systems—may still depend on high-end quartz OCXOs.
How do MEMS oscillators simplify system design?
MEMS timing solutions reduce design complexity and save board space by integrating resonators and oscillators into a single package. Unlike quartz, MEMS oscillators eliminate the need for external capacitors and complex matching circuits, enabling easier implementation in compact, high-performance systems.
What are the supply chain advantages of MEMS over quartz?
MEMS oscillators leverage standard semiconductor fabrication, reducing lead times compared to quartz, which requires specialized crystal cutting and tuning. They scale more efficiently, supporting high-volume production without quartz-related bottlenecks. Additionally, programmable MEMS oscillators can replace multiple fixed-frequency quartz SKUs, simplifying inventory management and minimizing supply chain risk.
Is MEMS the future of precision timing?
While both technologies will continue to coexist, MEMS is driving the future of precision timing, particularly in high-performance oscillators. The industry is rapidly adopting MEMS-based timing solutions for their flexibility, reliability, and scalability. However, quartz may still be used in lower- to medium-performance applications that don’t require precision timing, programmability, or real-time adaptability to dynamic environmental conditions. Similarly, certain niche applications demanding ultra-low phase noise and jitter may continue to rely on high-end quartz oscillators.
Silicon-based MEMS oscillators redefine precision timing, offering superior performance, reliability, and integration. As MEMS technology advances, it will increasingly replace quartz, enabling next-generation systems to achieve greater efficiency, lower power consumption, and improved flexibility. Contact the SiTime team today to learn more.